1. Introduction:
Since 2020, large format modules of various designs have emerged on the market. There has been confusion regarding the impact of large format modules on a PV power plant’s BOS cost and, given the potential misconceptions, LONGi has collaborated with DNV in the US on an analysis of boundary conditions and influencing factors involving such calculations.
DNV is one of the world’s leading certification bodies, providing testing, certification and technical advisory services to the energy value chain.
Three types of 500W+ module with fixed rack (2P, 4L) and tracker (1P) were compared in the analysis of BOS costs, assuming identical power plant design capacity and boundary conditions, with results indicating a slight difference among the three module types and a slight advantage of the 182-72c module, by virtue of its higher efficiency.
2. Scheme and principle of cost calculation:
This analysis involved 182-72c, 210-55c and 210-60c modules with front power of 500W +, and three comparison schemes under different racking structures were adopted:

Half-cut and MBB technologies were applied to all three module types. Due to silicon wafer dimensions, the Isc (short-circuit current) of the 182 module is less than 15A, while that of the 210 modules is greater than 18A. The 182-72c and 210-55c modules both have an area of about 2.6m2 and a weight of <33kg. Specific module information is listed in the table below, with module power based on the same cell efficiency under mass production, the efficiency of the 210 modules being slightly lower than that of the 182 module due to greater internal resistive loss under a higher current.

Based on theoretical analysis and historical experience, the design of racking, cabling model selection and labor are important factors influencing BOS cost. A large-scale power station with flat terrain was assumed in this calculation, together with the following three design principles, in order to ensure the fairness and universality of the results:
① Same length for fixed racking;
② Same cable power loss in selection of PV cable specifications
③ Same cost of installation per watt for the different modules (certain boundary conditions to be considered regarding size and weight of module, as the larger the module size, the fewer will need to be installed, but with a lower installation efficiency.)
A central inverter was adopted in the project design, with comparison to sub-arrays with a DC capacity of 3.7MW in terms of costs associated with racking and foundation, electrical equipment, manual installation and land.
3. Calculated results:
The table below lists the final results, indicating that the BOS cost of a 182-72c module is lower than that of a 210 module under these different racking configurations. For an installation with fixed racking, advantage in BOS cost of ¢0.1-0.3/W is achieved by the 182 module, with a greater advantage in the case of a 1P tracker scenario.

Scenario 1: 1P tracker
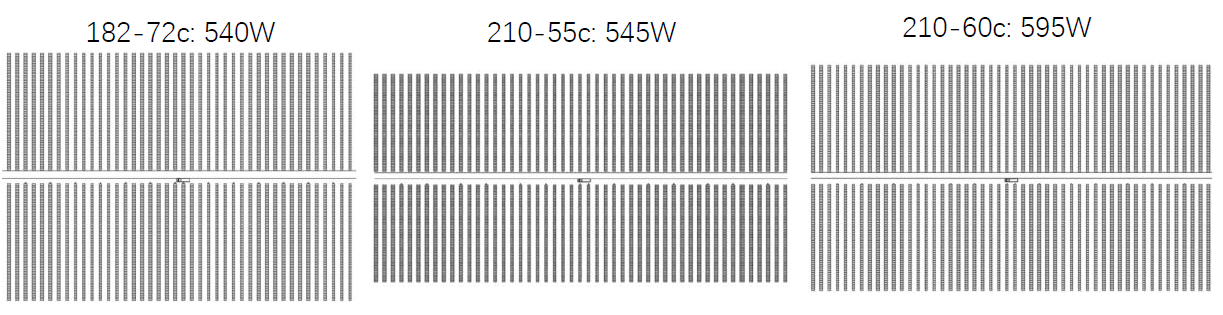
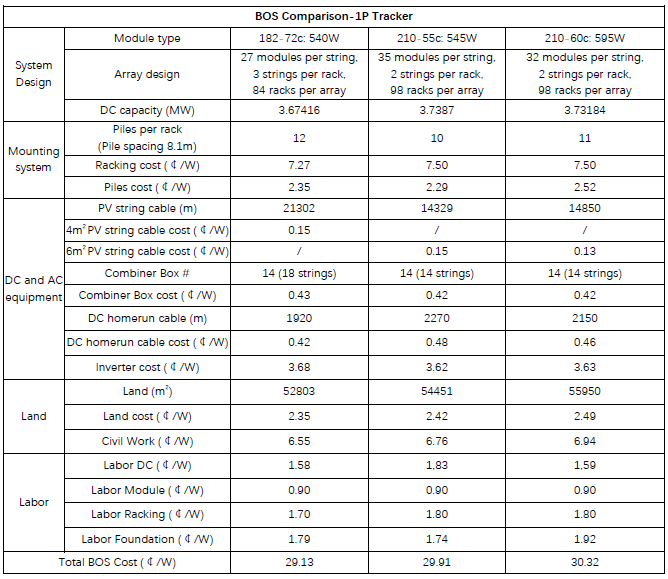
With a 1P tracker adopted, the BOS cost of the 182-72c module is lower than that of the 210-55c module by¢0.78/W and lower by¢1.19/W than that of the 210-60c module. The lower BOS cost of the 182 module is mainly attributable to the lower cost of tracker support (including labor cost) and land (including land cost and cost of civil work). The maximum length of a 1P tracker is 100m, with it able to carry 3 strings of 182-72c modules or 2 strings of 210 modules. The power capacity of a tracker using 182 modules is superior by almost 15% to when it uses 210 modules, meaning that savings can be made in steel consumption, motor and electrical control costs and labor cost per watt. As for land related costs, less trackers will be needed for the 182 module, with the smaller spacing achieved between tracker and module enabling higher efficiency, resulting in a saving of over 3% on the final area of land acquisition required.
Scenario 2: 2P fixed rack
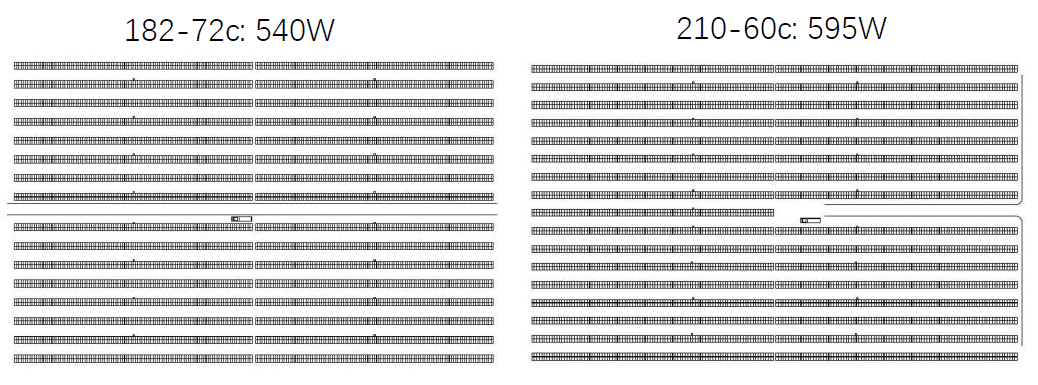
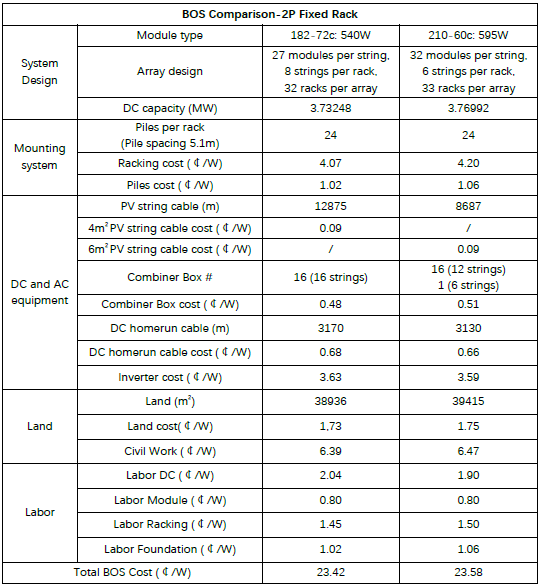
With 2P fixed racking adopted, the BOS cost of the 182-72c module is lower than that of the 210-60c module by¢0.16/W, due to reduced land and racking costs brought about by a difference in efficiency. By means of lengthening a single rack on a flat terrain, significant savings on the cost of racking and piles can also be achieved. However, the length of a single rack is limited to 120m due to restrictions in areas such as thermal expansion and contraction in steel structure, with a rack of this length capable of carrying 8 strings of 182 modules or 6 strings of 210 modules, either scenario resulting in the same level of total power. In terms of electrical costs, with the total capacity of combiner boxes consistent with the total combined current, there is little difference in combiner box and DC cabling costs. The above therefore supports the view that there exists a misconception that the higher the string power, the lower the costs associated with racking and electrical works will be.
Scenario 3: 4L fixed rack
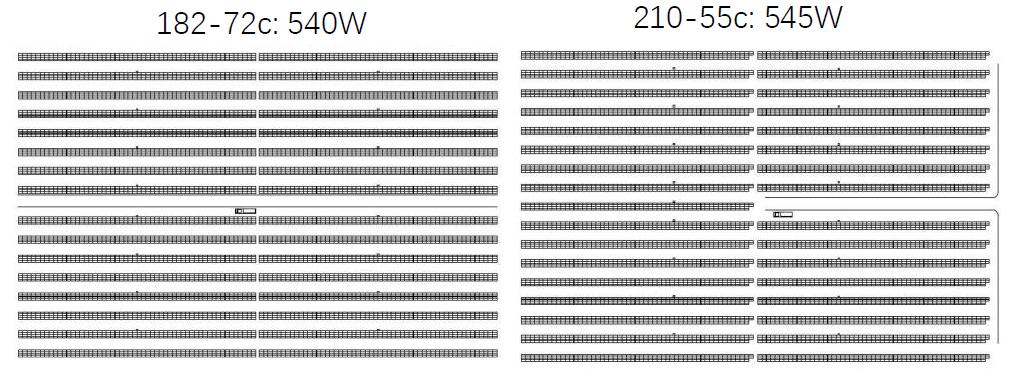
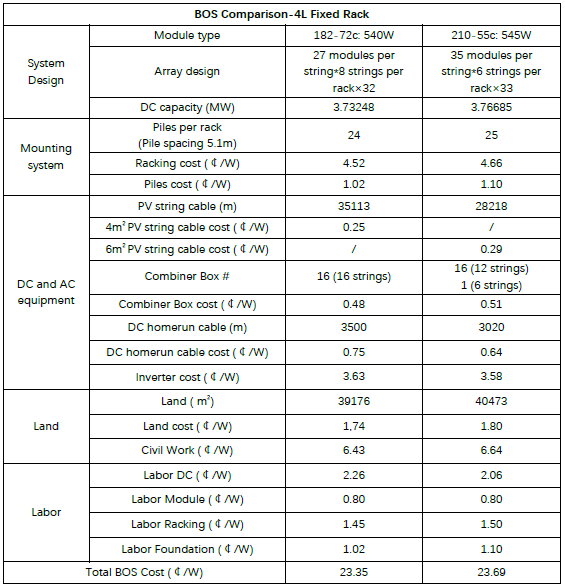
With a 4L fixed rack adopted, the boundary conditions are similar to those for the 2P fixed rack. However, there is a greater difference in land related costs as the efficiency of the 182-72c module is 0.27% higher than that of the 210-55c module, resulting in a superiority in BOS costs of up to ¢0.34/W.
4. Conclusions
The BOS comparison between three types of 500W+ modules carried out by DNV (project in Texas, USA) has proven that, under fair and practical boundary conditions of module power, capacity ratio, racking length, selection of electrical equipment and manual installation costs, the adoption of over-sized modules with an ultra-high current does not show advantage in BOS cost savings than 182-72c modules, as module efficiency is still the critical factor in BOS costs.
It should also be noted that this comparison was based on the same sub-array capacity. In reality, in the case of large power plants, land resources will usually be fully utilized to maximize installation capacity, meaning that 182 modules will represent a larger capacity (about 2 ~ 3%) with higher module efficiency, potentially saving on project development cost per watt and costs arising from booster stations and outgoing utility lines on the AC side, further strengthening the 182 module's potential superiority in overall value.
About LONGi
Founded in 2000, LONGi is committed to being the world’s leading solar technology company, focusing on customer-driven value creation for full scenario energy transformation.
Under its mission of 'making the best of solar energy to build a green world', LONGi has dedicated itself to technology innovation and established five business sectors, covering mono silicon wafers cells and modules, commercial & industrial distributed solar solutions, green energy solutions and hydrogen equipment. The company has honed its capabilities to provide green energy and has more recently, also embraced green hydrogen products and solutions to support global zero carbon development. www.longi.com