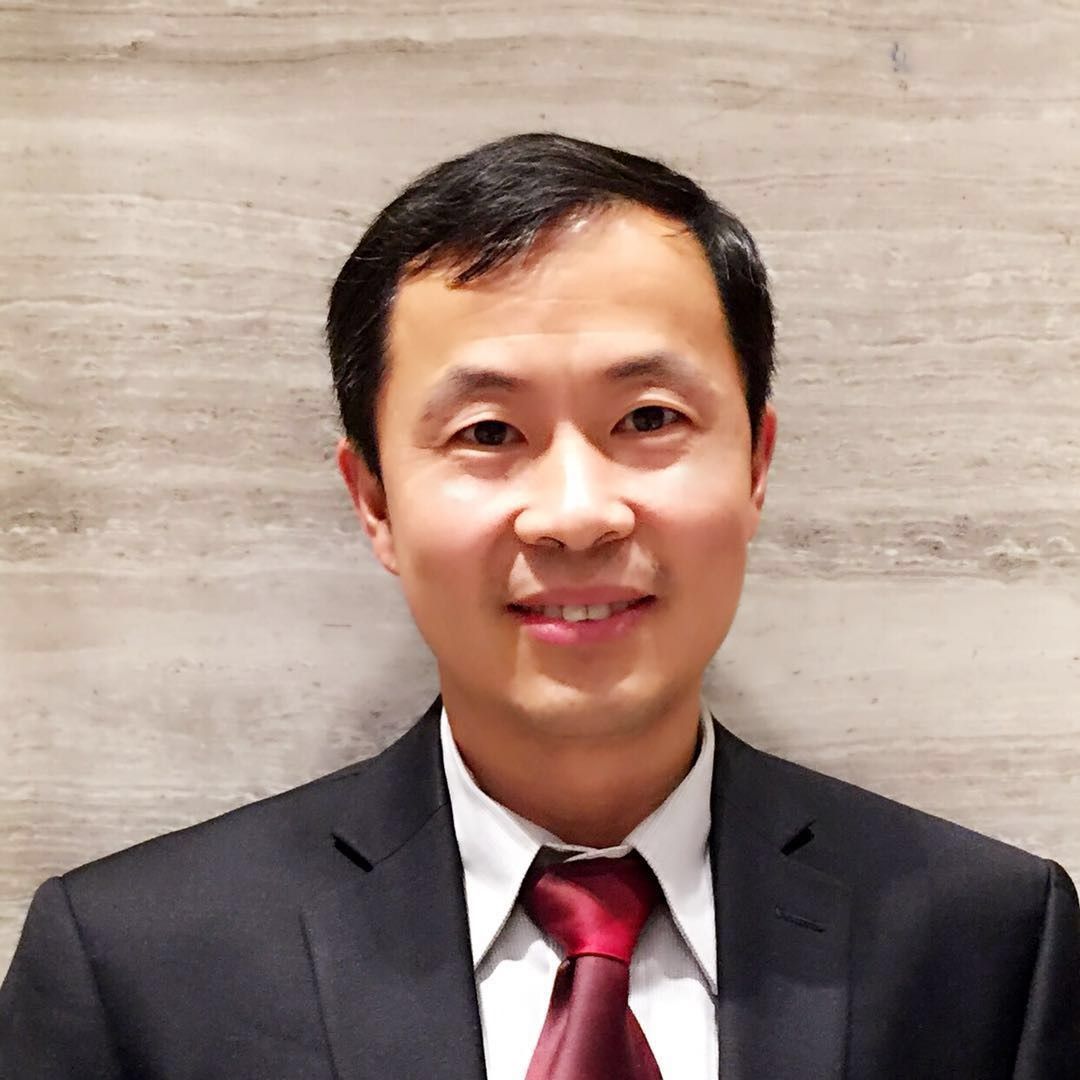
Dr Hongbin Fang, Director of Product Marketing at LONGi Solar talks about the “Technologies Behind the Innovations”
LONGi Solar has recently released the specs on its upcoming contribution to the ultra-high-power 500W-plus solar module market, the Hi-MO 5. The new module, which is due for commercial production in September 2020, is a high-power product ideal for utility-scale power plants. Dr Hongbin Fang, Director of Product Marketing at LONGi Solar talks about the objective and innovations behind the Hi-MO 5 technology, its applicability and key differentiators, timeline for commercial availability, and customer feedback.
What have been the key highlights of LONGi’s product development strategy so far in 2020?
LONGi Solar, at its core, is a technology- and innovation-driven manufacturer and the global PV market is rapidly moving towards high-power modules to reduce system costs and initial upfront capital investment. Our product development strategy has always been based on technology advancements and innovations that help our customers to achieve better system economics and lower LCOE.
Towards this end, the most significant breakthrough in 2020 has been the launch of Hi-MO 5 series of modules which are best suited for utility-scale solar applications. Our innovation logic for this new series of modules is to look at every aspect of PV project deployment with holistic view and find best overall solution: not only ingot, wafer, cell and module manufacturing processes, but also module deployment processes, such as transportation, installation and system integrations. Given the significant evolution of developing utility-scale PV projects globally, the primary objective of developing Hi-MO 5 series is to meet higher-quality and greater efficiency demand of the industry and to reduce the LCOE of a solar power plant. We are very excited that the introduction of Hi-MO 5 modules will enable our customers to dramatically reduce their PV projects BOS cost.
Can you elaborate on the key innovations on the downstream side of solar value chain?
Hi-MO 5 is based on M10 gallium doped monocrystalline wafers and uses smart soldering technology. The 72c module power reaches 540W, with an efficiency of more than 21%.
M10 is a new solar wafer size standard at 182mm width. This standard is established with thorough studies across the whole PV module manufacturing and deployment processes. One of the key limiting factors is opening height of 40’ container commonly used to ship modules across oceans. With modules packed at landscape configuration and double stacked inside 40’ container, the module width is limited at about 1130mm. and each solar cell width at 182mm. In June, LONGi and six other leading solar cell and module manufacturers came together to establish this new industry standard of wafer size M10. With M10 wafer size standardization, all players through the value chain now have a common platform to develop and optimize their individual equipment and process to realize optimum performance and lower cost. This standardization will help to deliver better value for our customers.
In 2020, LONGi and Shin-Etsu Chemical entered into a global patent agreement on gallium-doped technologies, which allows applications of LONGi’s products with gallium-doped technologies. LONGi optimized gallium-doped M10 standard silicon wafers (182mm) to produce a P-Type Mono PERC module with the lowest light-induced degradation (LID), improved attenuation performance and high power, all of which helps in delivering better values to our customers. To be specific - the first-year power warranty is an industry-leading 98% and linear annual attenuation is within 0.45% through 30 years lifetime. While gallium-doped silicon wafers are more expensive, we have been able to address this challenge through advances in technology and production scale.
Further, smart soldering has been used to increase module conversion efficiency – in this case by 0.3%. Our proprietary technology uses “integrated segmented soldering ribbons” that maximizes light capture and reduces the gap between solar cells. It helps reduce the tensile stress of the cell for better reliability.
What are the other key features of these modules and in which ways would a utility-scale project developer benefit from using Hi-MO 5?
The working current of LONGi Hi-MO 5 module is about 13A. Including bifacial gain, the operating current remains within the maximum input current range of the inverter, with no power generation losses. The module length is compatible with 1P and 2P horizontal single axis tracking systems. We will continue to work with inverter and racking companies to ensure compatibility with Hi-MO 5 modules.
Hi-MO 5 bifacial modules continue with “double glass with frame” design that provides sufficient strength for high load capacity and proven long-term reliability performance. The strength of the frame negates the need for a cross-beam, helping avoid any shading losses at the back of the module.
Comparing to Hi-MO 4, Voc of Hi-MO 5 modules are kept the same, which enables same number of modules per string. With each Hi-MO 5 module is 20% higher power than Hi-MO4, per string power output is increased by 20%, which will significantly reduce both mechanical and electrical BOS costs. With power rating per module is 20% higher on Hi-MO5, significant savings can also be realized on installation labor.
By estimation, Hi-MO 5 modules can save our customers US$0.01-0.02 /W on BOS cost comparing to Hi-MO4 modules, bringing about lower LCOE and better value. LONGi has partnered with more than 20 customers globally to verify the BOS savings, lower LCOE and better performance of Hi-MO 5 modules in real world applications.
Further, Hi-MO 5 will be backed by competitive warranties and LONGi Solar's commitment to high quality customer service.
What has been the primary response of LONGi’s existing and potential consumers to the new series? Which markets are likely to be the early adopters of this technology?
We have seen an overwhelming response from our customers across the world for the Hi-MO 5 series. While the production is scheduled from Q3 2020 onwards, we are already beginning to receive tremendous queries and orders which is a very positive sign.
As far as the markets are concerned, the product is likely to witness high uptake in large utility projects across regions due to its widespread suitability and cutting-edge benefits.
What is the company’s target regarding Hi-MO 5, both in terms of production capacity?
The module production capacity of LONGi has increased 20-fold from 1.5 GW in 2015 to 30 GW in 2020. Hi-MO 5 will be produced in volume and receive IEC/UL certification in September 2020. Its production capacity will reach 12 GW by end of 2020, guaranteeing a stable supply for global customers.
LONGi has been leading another key initiative pertaining to wafer size standardization. What is the idea behind that and what has been the progress so far?
For a long time uptil 2018, M2 wafers measuring 156.75mm were widely seen as the industry standard, representing more than 90 per cent of the market. The trend of larger photovoltaic modules began in the second half of 2018. At that time, monocrystalline modules using 158.75mm silicon wafers first appeared, together with silicon wafers with specifications of 157.4mm and 161.7mm, all larger than the mainstream M2-156.75mm wafer.
Since 2019 however, manufacturers have begun to see benefits in increasing wafer sizes, leading ultimately to modules rated at over 500 W appearing on the market. Given the compatibility with existing 100GW cell production capacity, M6 wafers of 166mm were duly launched in May 2019 by LONGi. Hi-MO 4 based on M6 wafer is suited for full scenarios such as C&I, large utility projects, through promotional activities, the downstream power plant investment and design sector recognized the system side value brought by the increase in wafer size.
With the absence of a common standard, companies have adopted wafers of varying sizes, resulting in an increase in manufacturing costs throughout the entire industry supply chain, including wafers, cells, modules and auxiliary materials such as glass. This situation has complicated customers’ selection processes, the installation of photovoltaic systems and coordination between the industry’s upstream and downstream sectors. To effectively address these issues and accelerate the industry’s efficient and standardized development, LONGi led a pack of seven solar manufacturers to establish the new M10 silicon wafer standard size (182mm x 182mm).
Besides LONGi, the group includes JinkoSolar, Canadian Solar, JA Solar, Runyang Yueda Photovoltaic Technology, Lu’an Solar Technology and Zhongyu Photovoltaic Technology. Our initiative to promote standardization will help optimize the use of resources and promote the photovoltaic industry’s continued healthy development. It will be good to have more manufacturers join the initiative.