The Group established a comprehensive occupational health and safety management system to create a safe production environment and culture, effectively safeguarding the occupational health and safety of employees. We have formulated internal administrative guidelines, including the Management System for Quality, Environmental, Occupational Health, and Safety Accidents, the Work Safety System, the Environmental Safety and Occupational Health Management Manual, the Occupational Health Management System, the Laborer Personal Protective Equipment Management System, and the Laborer Occupational Health Monitoring, Protection and Files Management System. Additionally, we have established the EHS Committee, representing all employees, overseeing our corporate work around occupational health and safety, and building a comprehensive and standardized production safety system. In 2023, our occupational health and safety system covered 100% of our employees, and 100% of formally commissioned manufacturing bases of our subsidiaries have been certified to ISO 45001.
In 2023, we further improved our safety management system by publishing 24 more management measures, including 4 Procedures, i.e. the EHS Incidents and Accidents Control Procedure, the Fire Control Procedure, the EHS Emergency Preparedness and Response Control Procedure, the Control Procedure of Environmental Safety Target Metrics and Management Plan, and 13 general standards, such as the EHS Education and Training Management System and Major EHS Hazards Management Measures, as well as 7 general policies, including Guidelines on Achieving “Three Simultaneities” in Building Project Safety and Occupational Disease Prevention Facilities, and EHS Risk Identification in Construction Projects.
Production safety
Guided by the production safety management principle of “safety first-comprehensive governance with a main focus on precaution”, LONGi has been working nonstop to strengthen safety ownership and responsibility. We set annual occupational health and safety management goals to implement production safety measures and ensure all work is healthy and stable. Under relevant policies, we set goals for occupational health and safety every year and take a goal-oriented approach to implement measures to safeguard production safety.
To effectively manage occupational health and safety risks in the production and manufacturing process, we engaged all employees in the identification and assessment of safety hazards, thus ensuring that risks in all steps, including engineering, silicon wafers, batteries, PV modules, and power plants are identified and controlled. Moreover, we instructed frontline teams to carry out risk control, emergency drills, examinations, and training to prevent accidents and incidents from happening.
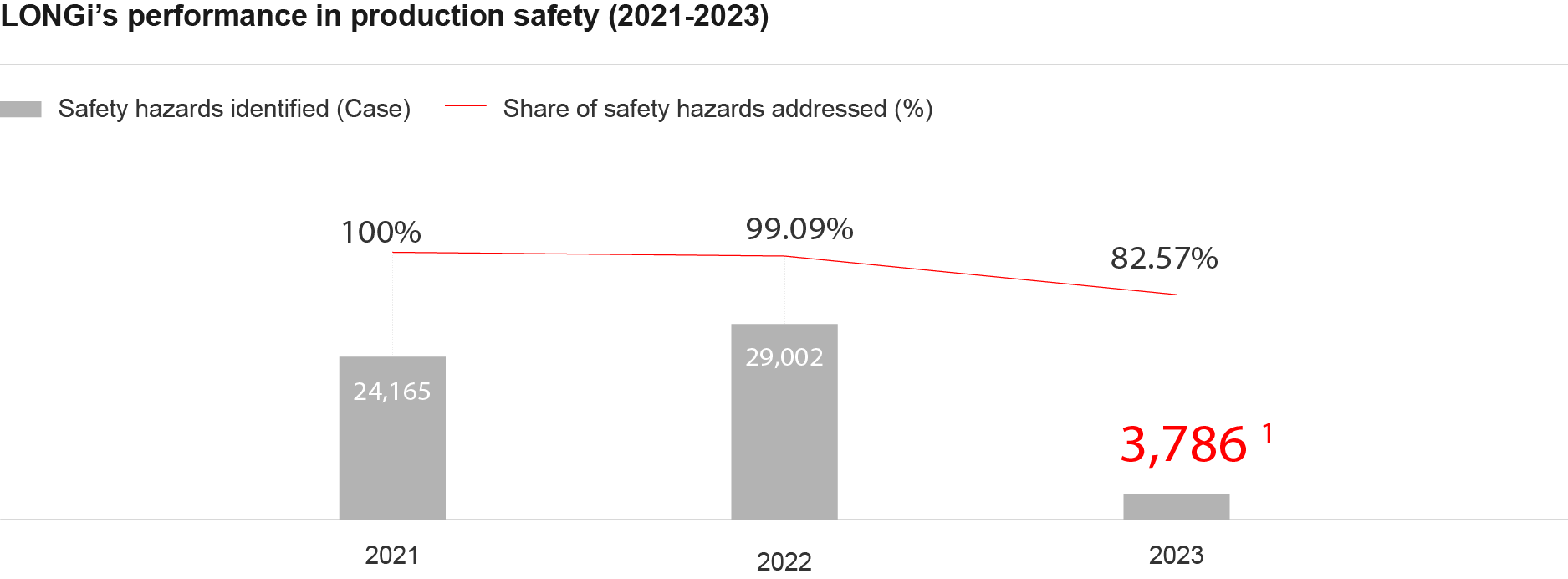
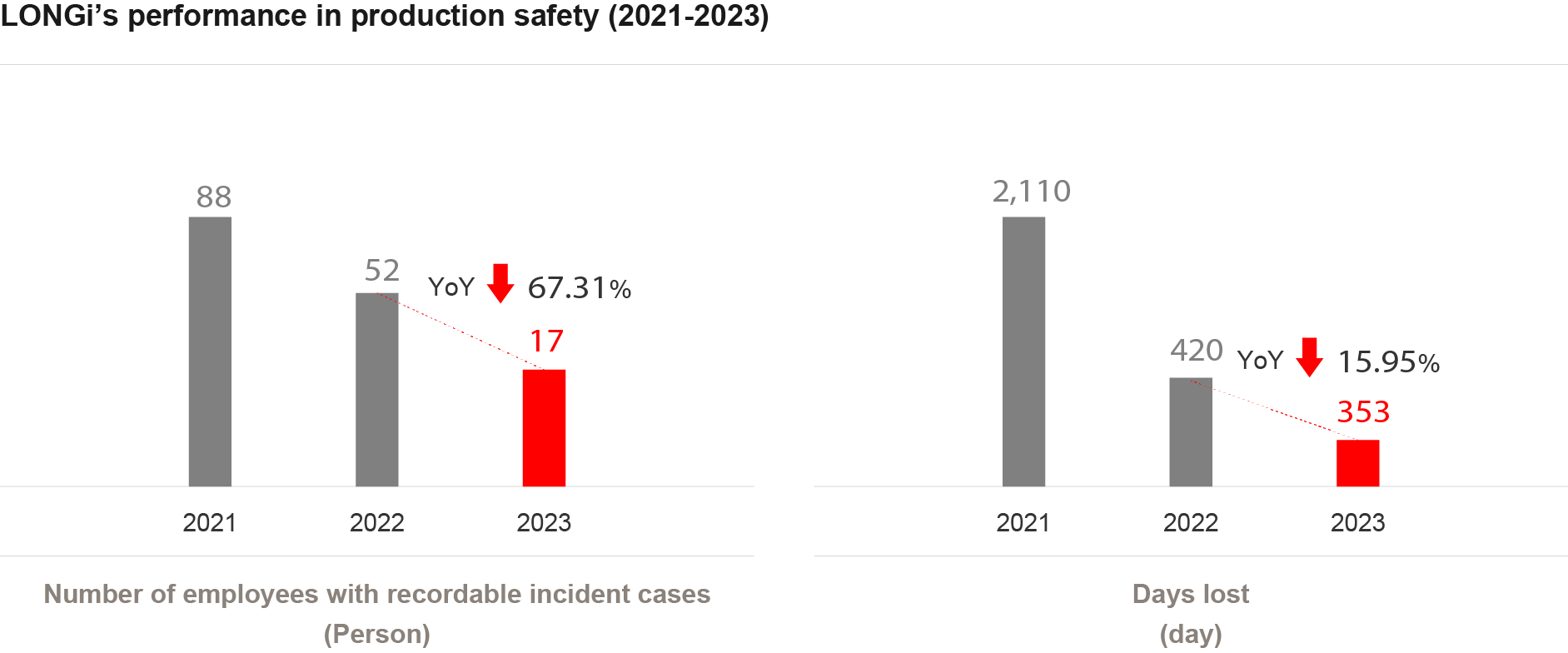